资讯
联系我们
公司名称:化工填料厂家
公司QQ:27749890
联系人:龙经理
业务电话:18779917026
联系地址:江西萍乡湘东陶瓷工业园
蒸馏技术在石油炼制工业中的发展与展望
2020-02-02 阅读:次
以蒸馏过程强化与节能为背景,在对塔盘、填料、分布器等塔内件技术发展分析的基础上,总结了我国蒸馏过程的大型化技术在石油炼制工业中的应用与发展,提出了采用新型碳化硅泡沫材料在塔盘及填料上的应用可大幅度提升精馏效率的思路。通过将低温余热发电技术与蒸馏过程进行耦合,实现了对于蒸馏过程低品位的有效利用,结合热耦合精馏、热泵精馏、多效精馏技术等节能措施,蒸馏过程的使用与回收变得更加科学与全面。新型材料传质元件和低温余热发电技术的开发与应用使绿色蒸馏概念在石油炼制行业的发展更迅速、有效。
随着国民工业对于石油产品及其下游产品的需求越来越大,对于资源利用大化和环境友好原则的要求不断加深,石油炼制工业在不断壮大和。“十一五”期间,国内的原油处理量已经增长至4.23亿t/a,“十二五”期间有望突破6亿t/a;炼油能力从2005年底的3.25亿t/a迅速增加至2010年底的5.04亿t/a,增长了55.1%。然而,随着世界性的原油下降,原油资源越来越匮乏,重质原油、高硫高盐原油成为各炼油厂的主要加工对象,原油处理变得越来越困难。另外,人们对于环境的要求日益突出,燃料油的标准也越来越高。为了达到要求,在原有的设备和技术基础上,炼油厂的单位产品能耗与日俱增,庞大的石油产品需求量以及巨大代价,给企业效益及效益带来巨大的冲击[1-4]。
蒸馏作为当今主要的化工分离技术,在石油炼制工业中占有重要地位。例如,在常减压分离、催化裂化和延迟焦化、轻烃单质分离等石油炼制工业的工艺工段中,蒸馏承担了绝大部分的分离纯化任务。蒸馏过程是热分离过程,较低的热力学效率决定了蒸馏过程需要消耗大量的,其能耗占整个分离过程的50%~70%[5]。世界炼油行业蒸馏过程大型化趋势明显,大的常减压装置单套规模已达到1800万t/a,催化裂化、催化重整、加氢裂化和焦化装置也分别达到了1000万、425万、400万和670万t/a[6]。目前,尽管国内的炼油企业经历了多年的努力已初具规模,但与炼油企业相比,普遍存在蒸馏设备单套规模小、装置构成复杂、能耗较高等问题,蒸馏过程大型化已成为国内石油炼制工业的主要发展趋势。
近些年,为了提高产能和降低单位产品的能耗,科研工作者针对蒸馏设备大型化的关键技术和过程强化与节能技术进行攻关,蒸馏设备大型化的关键理论与技术也在不断更新并取得突破。同时,多种新型高效率塔板和填料的应用,配合系统综合利用的节能措施,也大大降低了单位产能的能耗。以提高单系列设备效率和系统综合利用为核心的绿色蒸馏过程理论也是当今蒸馏技术发展的重点课题。笔者重点介绍近些年国内蒸馏过程大型化技术在石油炼制行业的发展,主要包括塔盘、填料、分布器、支撑等塔内件技术的研发与应用;诠释绿色蒸馏过程概念,并展望新型泡沫传质元件和低温余热发电技术在蒸馏过程的应用前景。
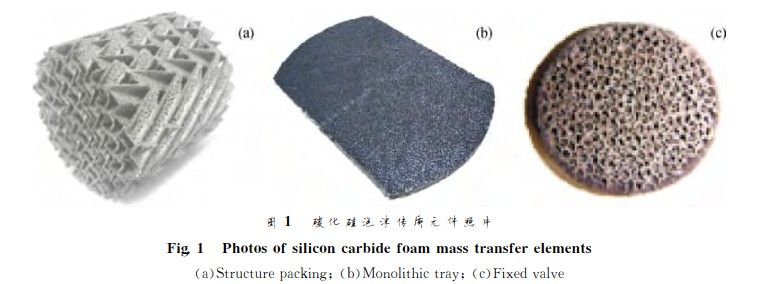
1 蒸馏过程大型化技术在石油炼制工业中的发展
1 .1 蒸馏过程大型化技术重点概述
蒸馏设备直径以后,其效率随之下降,从而产生设备大型化所共有的放大效应。蒸馏设备大型化的难点在于,如何解决好放大效应及长期运转所带来的震动、堵塞等问题。具体来说,蒸馏设备大型化研究过程中主要遇到的问题有:
(1)分布问题,大型化带来的突出问题是气、液相分布不均,这是塔内的气、液相流动、传质、传热效率主要因素;
(1)分布问题,大型化带来的突出问题是气、液相分布不均,这是塔内的气、液相流动、传质、传热效率主要因素;
(2)长周期运行问题,精馏塔长周期运转要解决设备稳定性和堵塞结焦问题,以免影响装置正常运转;
(3)大型化的力学问题,塔器大型化需要解决内构件支撑结构静态力学强度、刚度和长期处于受热状态的热变形及变形问题。针对以上问题,国内相关科研人员进行了长期的研究和实践,研究的主要方向也集中在新型塔盘、高效填料、液体分布器、气体分布器、支撑技术这几个关键塔内件技术上[7-8]。
(3)大型化的力学问题,塔器大型化需要解决内构件支撑结构静态力学强度、刚度和长期处于受热状态的热变形及变形问题。针对以上问题,国内相关科研人员进行了长期的研究和实践,研究的主要方向也集中在新型塔盘、高效填料、液体分布器、气体分布器、支撑技术这几个关键塔内件技术上[7-8]。
1.2 数字化设计技术的发展
数字化设计是运用计算机图形学和图像处理技术,将科学计算过程中产生的数据及计算结果转换为图形或图像并进行交互处理的理论、方法和技术。数字化设计改变了传统的设计方法,旨在利用计算流体力学、模拟计算等手段实现精馏塔以及塔内件的参数化,并将参数模型导入有限元分析软件,对精馏塔塔体和塔内件以及支撑结构在外界载荷的作用下以及不同的操作工况的强度、刚度、稳定性和可靠性给出精确的校核计算[9-12]。
相比于传统的实验和经验为主的设计过程,数字化设计过程具有容易改变参数、不受条件限制、耗时短、减少人力物力投入等点,这不为设计过程节省了时间和费用,也间接地为企业创造了经济效益。在蒸馏设备大型化的过程中,数字化设计主要应用在塔板、规整填料、分布器、支撑元件的结构设计上。通过改变物理模型中的几何参数,观察所设计结构中的流体力学及力学性能数据,从而筛选出较的塔内件结构[13-14]。Li等[15]、刘德新等[16]、李瑞等[17]和王晓玲[18]对塔板上的气、液相流动进行了仿真模拟,给出了接近真实的模拟结果。
陈保卫等[19]和周永生等[20]用Fluent模拟了规整填料塔内的气、液相流场分布情况,与所观测到的实际情况基本相符。金红杰等[21]和刘德新等[22]模拟了双切向气分布器中的气、液两相流的流动状况,并对多种分布器进行了性能比较和结构改进。如今,很多国内外学者已经习惯于先将要设计的新型塔内件进行数字化设计,再将得到的结果进行实质性物化试验,在这方面的文献报道屡见不鲜。
虽然数字化设计技术给设备设计过程带来了很大的便利,并节省了一大部分设计投入。但由于传递理论的不成熟以及计算机技术的局限,数字化设计的可信度还是不能和实践经验相提并论。数字化设计的结论能作为参考使用,设计的真实效果还需要实践来检验。相信在不远的将来,随着传递理论越来越能描述实际现象,计算机技术取得突破发展,数字化设计会提供完全可靠的设计参数,将设计方面的投入降到低。
1.3 塔内件重点技术革新
近些年,国内的塔内件技术取得了突飞猛进的发展,使得我国化工产品能耗逐渐降低,分离效率显著提升,有的技术已经达到水平。
1.3.1 塔盘技术的革新
塔盘技术的革新主要集中在开孔结构的设计上。
目前,国内的研究重点主要集中在浮阀及固定阀的结构设计上。华东理工大学以条形浮阀为基础,相继开发了组合导向浮阀塔板[23]、B型导向浮阀塔板[24]、组合波纹导向浮阀塔板[25]、HLFV浮阀塔板[26]等,这些新型浮阀塔板均能有效地塔板上的液体返混,减小液面梯度,传质效果。浙江工业大学以MD塔盘为基础开发的DJ系列塔盘,
采用矩形悬挂式降液管,主要适用于处理高液/气比、大液量的精馏和吸收等操作过程,处理能力比一般塔板高30%~50%。通过在受液区增设导流装置和防冲击漏液装置,采用新型固定阀作为鼓泡元件以及在塔板下方复合填料的措施,改善板上液流分布,减少冲击漏液量和雾沫夹带量,从而大大提高塔板效率,操作弹性[27]。清华大学化工系结合固定阀和浮阀塔板的缺点开发了一种两者相结合的高性能自适应浮阀塔板———HAVTH塔板[28]。
该塔板由MVG固定阀塔板和Surface微分浮阀塔板组合而成,其设计充分利用塔板上方的传质空间,提高塔的操作弹性;如果将整体形状改成梯形,还能够起到推动液体的作用。河北工业大学专注于立体传质塔盘(CTST)的开发与应用,所研发的一系列CTST塔盘已经在医药行业及传统化工分离工段得到广泛应用。CTST塔板采用矩形开孔,开孔上方安装带筛孔的梯形喷射罩和分离板,充分利用了板上的传质空间,使得CTST塔板拥有操作弹性大、板效率高、处理量大、物性适应性强、压降低等特点[29-31]。石油大学综合导向条阀和MMVG固阀的点,开发了双层导向浮阀塔板[32]和SFV全通导向浮阀塔板[33]。
2种浮阀塔板都是在条形浮阀阀面上开设微型固阀,同时具备两者的良特性,并且在阀腿上都开有导向孔。这样可以加快塔板上液体流动,降低塔板上液面梯度,消除塔板两端液体停滞区,改善塔板上液体流动力学与传质性能。北京化工大学侧重于新型筛板塔的研究与应用,设计的导向筛板塔板不但保留了筛板塔传质效率高、结构简单等特点,还在一定程度上加大了操作弹性和处理通量,为筛板塔的应用提供了更广阔的空间[34]。天津大学主要以条形浮阀和固定阀为基础,进行新型塔盘的开发[35-38]。近期,石化工程建设公司与天津大学合作开发的一种新型流线型导向固定阀塔板,其特点就是具有平滑的弯曲折边,液体流动呈流线型,而且阀上面具有推液作用的导向孔。实践证明,这种塔盘能够很好地分配气、液流场,具有低压降、液面差小、传质效率高等特点,以及具有能够装备大型塔器的条件[39]。
2种浮阀塔板都是在条形浮阀阀面上开设微型固阀,同时具备两者的良特性,并且在阀腿上都开有导向孔。这样可以加快塔板上液体流动,降低塔板上液面梯度,消除塔板两端液体停滞区,改善塔板上液体流动力学与传质性能。北京化工大学侧重于新型筛板塔的研究与应用,设计的导向筛板塔板不但保留了筛板塔传质效率高、结构简单等特点,还在一定程度上加大了操作弹性和处理通量,为筛板塔的应用提供了更广阔的空间[34]。天津大学主要以条形浮阀和固定阀为基础,进行新型塔盘的开发[35-38]。近期,石化工程建设公司与天津大学合作开发的一种新型流线型导向固定阀塔板,其特点就是具有平滑的弯曲折边,液体流动呈流线型,而且阀上面具有推液作用的导向孔。实践证明,这种塔盘能够很好地分配气、液流场,具有低压降、液面差小、传质效率高等特点,以及具有能够装备大型塔器的条件[39]。
1.3.2 填料技术的革新
规整填料是大型塔器传质元件的选。理想的规整填料应具有压降小、分离效率高、操作弹性大、适应性强、放大效应小等特点。压延刺孔波纹板填料是将金属薄板先辗压出密度很高的小刺孔,再压成波纹板组装而成的规整填料。由于金属压延刺孔波纹板表面特殊的微刺孔结构,它的毛细作用加强,润湿性能提高,分离性能良好,因此具有较好的传质效率[40]。板网波纹填料是用金属薄板经冲切拉伸而成的金属板网(或网孔板)加工成的波纹填料。金属板网表面的菱形孔容易使液体在其表面形成液膜,在良好的条件下,实际传质表面积可大于金属本身的表面积,且液体膜受板网表面影响产生湍动混合与表面更新,因而提高了板波纹填料的传质效果[41]。
清华大学研究开发的新型复合填料,是在规整填料基础上采用交错90°排列的水平波纹(PFG)组合而成。PFG本身是填料,同时又起到分布器的作用,具有良好的自分布性能,传质效率比规整填料提高15%~20%。每米填料的理论板数比同规格的Sulzer填料高15%左右[42]。天津大学自主开发了组片式(Zupak)和峰谷搭片式(Dapak)波纹填料。2种填料都是以金属波纹板填料为基础进行改造而成,具有良好的流体力学和传质性能,与相应型号的Mellapak相比,分离效率和通量都有不同程度的升高,目前两者都已成功在石油化工行业中广泛使用[43]。
清华大学研究开发的新型复合填料,是在规整填料基础上采用交错90°排列的水平波纹(PFG)组合而成。PFG本身是填料,同时又起到分布器的作用,具有良好的自分布性能,传质效率比规整填料提高15%~20%。每米填料的理论板数比同规格的Sulzer填料高15%左右[42]。天津大学自主开发了组片式(Zupak)和峰谷搭片式(Dapak)波纹填料。2种填料都是以金属波纹板填料为基础进行改造而成,具有良好的流体力学和传质性能,与相应型号的Mellapak相比,分离效率和通量都有不同程度的升高,目前两者都已成功在石油化工行业中广泛使用[43]。
近些年,设计人员对规整填料进行开孔和开窗,并将金属板进行波纹化,尝试金属丝网双层化、金属板和金属丝网组合叠放等改进。结果表明,填料对于气体的分布更加均匀,并可形成更大的传质表面,提高了传质效率。同时,设计者将直线波纹进行曲线化,降低了气相局部速率,减小了局部涡流,使压降降低[44]。
1.3.3 分布器技术革新(1)液体分布器
大型塔器的液体分布器需具有更高要求的液体均布和抗堵塞性能。针对以上目的,在槽式液体分布器基础上,开发了新型多级槽式液体分布器。分布器一级槽采用全联通结构,二级槽增设整流导流挡板结构。一级槽的全联通结构能够消除液面落差和主槽之间的偏流,保证槽内水平度;二级槽加设整流挡板,实现了液体分布器的线分布。这种设计既对液体分布质量有要求,又保证了长周期运行的工程要求。大型槽式液体分布器的预分布管设计非常重要。,普通等孔径预分布管内呈现两端流量大而中部流量小的特点,这会严重影响二级槽式分布器内的液体分布均匀性。天津大学采用实验和理论模拟相结合的方法,设计开发了变孔径的预分布器。这种预分布器的开孔呈现中间孔径大、两端孔径小的特点,使整个预分布管的流量均匀,解决了超大型分布器的初始分布问题[45]。
基于盘式分布器开发的导液盘式液体分布器,国内习惯叫做槽盘式液体分布器,也成功运用在大型塔器上。分布器底圈固定在塔圈上,在塔盘开矩形升气管,升气管侧壁中、上部开布液孔,同时增加导液管。槽盘式液体分布器主要是为了解决多级槽式液体分布器在安装空间高度和抗阻塞的缺陷而设计的。该分布器的点是占用空间小,集液体收集、分布、侧线采出于一体,而布液孔的高位设计使得重脏物有时间也有空间沉降于盘底。全联通结构设置不影响气体分布,使气、液相分布均匀,抗阻塞、防雾沫夹带性能越,操作弹性大。该种分布器的缺点是,对安装要求严格,容易漏液,适应于大液量的场合[46]。
(2)气体分布器
(2)气体分布器
大型炼油减压塔多为低压降的填料塔,直径达到10多米,而床层2m左右。这种低压降、大直径、浅床层塔器气体的初始分布对于塔器的正常操作和气-液的传质传热有很大影响。常用的气体分布器有双切向环流气体分布器、辐散式进气初始分布器、三维复合导流式初始分布器、双列片进气初始分布器等。其中,双切向环流气体分布器气体分布均匀,压降小,雾沫夹带低,与各种气体分布器相比具有较好的综合性能,在大型塔器中尤其是大型减压塔中应用较为广泛。近些年,对于双切向环流气体分布器的结构化成为研究的重点。主要是依靠CFD软件模拟针对导流板和套筒的参数设置来化分布器的气、液流场,从而使得大直径的塔器可以地发挥填料的效率,进料闪蒸空间高度也大大降低。这种分布器已广泛应用于较大直径(大于
4.0m)的塔中,如炼油装置减压塔、乙烯装置的油洗塔和水洗塔[45]。双层折返流气体分布器可以克服切向环流分布器气相环形通道上方气体分布不均的缺点,上层折返气体可以使气相分布更加均匀。
1.3.4 支撑技术革新
大型塔器中由于塔内件质量增加,气、液流场强度更高,同时还需满足长周期运行的要求,因而对支撑结构强度、刚度以及耐久度提出了更高的要求。普通的工字梁和槽钢支撑梁,在荷载的作用下自身变形,难以满足工艺的要求。借鉴铁路桥中桁架梁的设计思路,石化工程建设公司与天津大学合作,设计出大型塔用桁架支撑梁。这种支撑梁的桁架梁和支撑构件之间形成三角稳定结构,根据三角形的稳定性原理,可以有效地加强支撑梁的强度,减小支撑梁在负载时的挠度,同时提高整个桁架支撑梁的通透性,可以改善气流旋流的冲击,大大降低空间高度;与普通工字钢梁相比,可使气体实现横向混合,减少气相流动阻力,同时可减少金属材料的使用量[46]。
2 石油炼制工业中绿色蒸馏过程
2.1 绿色蒸馏过程概念
经过多年来精馏技术的众多实践经验,绿色蒸馏过程的概念逐渐形成。绿色蒸馏过程就是通过采用增加单系列蒸馏设备处理量及效率、提高蒸馏过程利用率、健全过程回收体系等手段,达到蒸馏过程节能减排、绿色的目的。从外在形式上看,绿色蒸馏过程概念的核心内容是蒸馏过程的强化与节能。
蒸馏过程的强化主要指精馏设备的强化和精馏工艺的强化。精馏设备强化指的是,采用高效的塔内件大幅度提升分离能力和处理能力,降低压降,进而间接实现精馏系统的节能。近些年,高效率塔板及填料层出不穷,使精馏塔的效率有了很大提高。同时,新材料在塔内件设计和制造方面的应用,使得精馏设备的强化过程不再拘泥于塔内件结构的改造;依靠新材料对力学、传质传热、空间利用度的性能提升,是以后精馏设备强化的新方向。精馏工艺强化主要指的是,精馏过程与反应的耦合(催化精馏)、精馏过程与其他分离过程的耦合(膜精馏)、精馏过程外场强化(微波场、超重力场以及超声波场)等[47]。目前,这几种精馏过程强化手段都处在快速发展阶段。
蒸馏过程的节能措施主要指的是工艺节能、流程节能、系统节能等[48]。其中,工艺节能是蒸馏过程节能的重要手段,包括改进工艺生产流程,采用技能新工艺、新技术等,典型的节能工艺包括热泵精馏、多效精馏、热耦合精馏等;流程节能主要指通过改变蒸馏系统的分离序列来改变蒸馏系统的生产工艺流程,进行和流量的合理匹配与耦合,减少流股,大限度地减少不可逆过程,从而达到节能的目的;系统节能[49]是指从整个系统全局考虑的转换、回收与利用等。在过程系统和热力学分析2大理论的发展及其结合与的基础上,产生了系统节能的理论和方法,在工程应用中取得了巨大经济效益。
蒸馏过程的强化与节能一直是国内外学者的研究重点,也取得了很多成果。其中,天津大学开发的碳化硅多孔泡沫填料和塔板作为一种新型塔内件受到广泛关注;同时,将低温余热的高温热泵和低温发电技术引入到蒸馏过程回收过程设计中的理念也为系统节能寻找到了新的契机。
2.2 碳化硅泡沫传质元件
碳化硅泡沫是一种具有均匀三维网状结构的特殊多孔陶瓷。其孔道分布均匀、开孔率高、相对密度小、比表面积大,对气体和液体介质有选择透过性,具有较好的吸收和阻压特性,以及良的热、电、磁、光、化学等功能[50]。碳化硅泡沫陶瓷除了拥有多孔陶瓷的特性外,还具有碳化硅本身的耐高温、、耐腐蚀、热膨胀系数小、热导率大、硬度高、抗热震等良性能以及半导体性征[51]。以上特点的整合,使碳化硅泡沫具有成为新型高效率传质元件的潜质。结合在塔内件与碳化硅泡沫材料研究上各自的势,天津大学和科学院金属研究所共同开发了一系列碳化硅泡沫规整填料和塔盘,并进行了大量相关性能测试和工业应用示范工作。图1是碳化硅泡沫传质元件照片。
2.2.1 碳化硅泡沫规整填料
碳化硅泡沫规整填料(见图1(a))是仿照波纹规整填料的形式而制得。水力学实验结果表明,与相同形式的金属丝网和金属板波纹填料相比,碳化硅泡沫规整填料的干、湿填料压降相当,持液量较大,在不同喷淋密度下的泛点气速较大,所以碳化硅泡沫规整填料的通量高,不易液泛。对其使用环己烷-正庚烷物系进行填料传质性能测试的结果显示,碳化硅泡沫填料的等板高度低、传质效率高,在相同喷淋密度下,其理论板数是同规格金属丝网波纹填料的1.5~2倍[52-54]。
2.2.2 碳化硅泡沫整体塔盘
碳化硅泡沫整体塔盘(见图1(b))是类比筛板塔盘而设计的一种微分塔盘。碳化硅泡沫整体塔盘充分利用塔盘面积,并将气相流动微,提供了很高的气-液相界面强度。从水力学和传质实验得出,相比于传统的筛板塔盘,碳化硅泡沫整体塔盘具有压降低、不易漏液、雾沫夹带量小、传质效率高等点,是一种整体性能良的蒸馏塔板[55-56]。
2.2.3 碳化硅泡沫固定阀塔盘
碳化硅泡沫固定阀塔盘(见图1(c))是将多孔碳化硅泡沫材料制成的圆形或矩形固定阀传质元件,取代F1浮阀镶嵌到塔盘的圆孔或矩形孔中而成。研究表明,在开孔率相同的情况下,相比于F1浮阀塔盘,碳化硅泡沫固定阀塔盘拥有更高的相界面强度,操作弹性更大,漏液量小,雾沫夹带量大大降低,传质效率大幅提高[57-58]。
碳化硅泡沫这类新型功能材料应用于蒸馏过程,能够显著气-液相界面强度,改善气-液接触的均匀性,在改良低气/液比体系的传质效果、催化蒸馏等方面发挥了重要作用。
2.3 低温热发电技术在蒸馏系统中的应用
低温热发电技术是基于朗肯热力学原理,利用中低温余热进行发电的技术。低温发电技术一经推出便得到了大范围的工业运用,例如地热发电、水泥厂低温余热发电、炼钢厂低温余热发电等。随着朗肯和Kalina理论的发展与健全,人们不但可以使用不同温位进行发电,并且能够进行发电的低温位也在逐渐降低[59]。天津大学研制的低温双全流发电机组可将低发电温度降至55℃。此套装置已经实现大型化生产,单机规模可达500kWh[60]。
在化工流程中,反应和分离过程产生各种各样的热量,不同的工艺过程其热量温位差异很大,可从几十度到几百度不等。现代流程工业靠热联合和热匹配能够回收利用大量的,但仍然有相当大量的低温热量需要经过空冷和水冷降温后,才能送往下一个工序或者作为产品储存。而对于蒸馏单元,塔顶冷凝器中冷却水移走的低温余热和塔底处的低温产品余热的回收与高效利用,会给蒸馏过程带来巨大的节能效益。将低温发电技术运用于蒸馏过程的低温回收,意味着蒸馏过程中高、中、低余热利用理念基本健全。
天津大学针对低温余热发电技术与蒸馏过程的耦合过程开展研究[61]。
他们以乙醇-异丙醇精馏工艺为基础,改造原有精馏设备,用发电机组替代原有系统中的冷凝器,形成以发电机组为冷凝装置的新流程,如图2所示。在新的精馏过程中,塔顶上升的蒸气直接进入发电机组的蒸发器侧,工质膨胀后的乏气进入冷凝器成为饱和液体,由工质泵加压进入蒸发器,完成。而蒸气被工质吸收热量后冷凝成液体进入储液罐中,一部分回到精馏塔中,一部分作为产品采出。
他们以乙醇-异丙醇精馏工艺为基础,改造原有精馏设备,用发电机组替代原有系统中的冷凝器,形成以发电机组为冷凝装置的新流程,如图2所示。在新的精馏过程中,塔顶上升的蒸气直接进入发电机组的蒸发器侧,工质膨胀后的乏气进入冷凝器成为饱和液体,由工质泵加压进入蒸发器,完成。而蒸气被工质吸收热量后冷凝成液体进入储液罐中,一部分回到精馏塔中,一部分作为产品采出。
研究结果表明,发电机组成功取代了塔顶冷凝装置,塔顶低温蒸气实现冷凝的同时,将通过发电机组部分转化为电能。低温发电机组在乙醇-异丙醇实验体系中,年均理论发电效率约为10.2%,实际发电效率约为4.2%。由此可见,精馏过程与低温发电技术的耦合可行,并且具有巨大潜力和经济效益。大限度地回收利用精馏过程中产生的余热进行发电,对响应节能减排措施和可持续发展战略具有重大意义[61]。
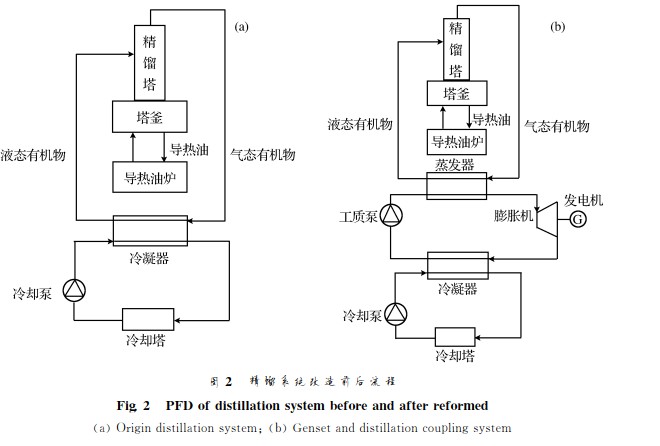
3 总结与展望
原油处理量逐年增加,能源问题日益严峻,蒸馏设备的大型化以及蒸馏过程强化与节能是解决此类问题的关键途径之一。塔内件技术的发展与应用是解决蒸馏设备大型化问题的关键所在,而数字化设计过程为塔内件及其他设备的设计节省了人力和物力,是以后设备设计技术发展的重点。
绿色蒸馏过程概念基本形成,提高单系列蒸馏效率、健量科学利用及回收体系是实现绿色蒸馏过程的基本途径。其中,新型碳化硅泡沫填料与塔盘的开发与利用为蒸馏过程的强化提供了新的方向,而低温余热发电技术的应用为蒸馏过程的节能提供了新的契机。
以节能减排、绿色为目的,以提高单系列分离效率、健量多级利用及回收体系为手段,绿色蒸馏过程概念作为指导蒸馏技术革新的理论依据,需要突破传统认知的框架,不再局限于原有蒸馏理论和实践经验,寻找类似于碳化硅泡沫这种新型材料及形式扩充塔内传质空间,改善气、液流动,以达到对蒸馏过程强化的目的。运用低温余热发电、高温热泵技术等转化技术,实现对于蒸馏系统低品位进行回收利用,研究热耦合、热泵、低温余热发电技术与蒸馏过程配合使用时的使用范围,创建蒸馏系统集成及回收理论,将能耗降至低,从而形成绿色的蒸馏过程,是未来蒸馏技术发展的方向。
